Frequently added aluminum alloy elements are aluminum, copper, magnesium, cadmium, lead, titanium, and other ultra-low temperature zinc alloy materials. Zinc alloy material dissolution point is low, good circulation, easy arc welding, fiber welding and plastic deformation production processing, corrosion resistance in the air, disability material is conducive to the acquisition and remelting; but stress relaxation compressive strength is low, easy to produce course aging caused by specification transformation. Melting method of production, aluminum die-casting or working pressure production and processing into talent. According to the manufacturing process can be divided into forging zinc alloy materials and deformation zinc alloy materials. What are the effects of adding various chemical elements to zinc alloy materials?
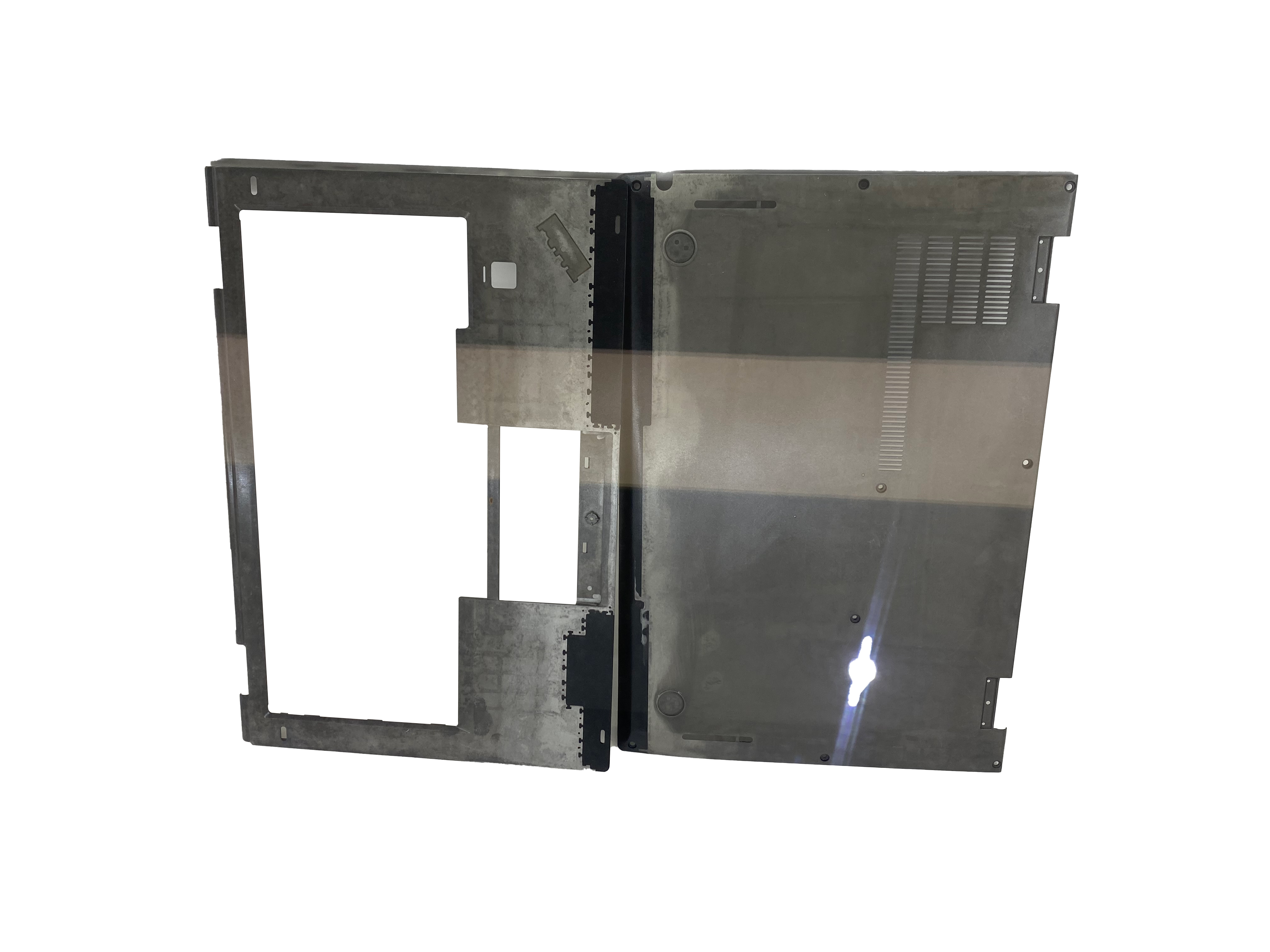
The role of copper
- Increase the strength and compressive strength of aluminum alloys;
- Improves the wear resistance of aluminum alloys;
- Reduce stress corrosion.
Disadvantages:
- When the copper content exceeds 1.25%, the specification and impact toughness of cast parts will be changed due to aging;
- Reduce the ductility of aluminum alloy.
The role of zinc alloy die-casting magnesium
- Reduce stress corrosion
- Optimize the mechanism of aluminum alloy, and thus improve the compressive strength of the aluminum alloy
- Improve the wear resistance of the aluminum alloy
Disadvantages:
- When the magnesium content is>0.08%, it causes thermal embrittlement, ductility reduction, and circulation reduction.
- Easily depleted by air oxidation in the molten state of aluminum alloy.
Residual primary elements
Lead, cadmium, and tin make the zinc alloy material stress corrosion becomes very more sensitive, to the temperature, and wet natural environment to accelerate their stress corrosion, reduce physical properties, and cause the specifications of the casting parts shift. When the zinc alloy material in the residue element lead, cadmium composition is too high, the product workpiece just aluminum die-casting forming, process performance all normal, but in indoor temperature storage for a period of time (eight weeks to a few months), the surface layer appears bulging.
The efficacy of aluminum
- Improve the forging characteristics of zinc alloy die-casting, enhance the flow of aluminum alloy, optimize the crystal, causing solid solution strengthening, and enhance physical properties.
- Reduce the reaction ability of zinc to iron and reduce the corrosion of iron raw materials such as goosenecks, abrasives, and clamp pots. Aluminum composition is manipulated at 3.8 to 4.3%. The key is to fully consider the specified compressive strength and circulation. Good circulation is an essential criterion to get detailed, precise specifications and surface finish casting parts.
Zinc alloy die-casting, residual elements: iron
- The reflection of iron and aluminum produces Al5Fe2 intermetallic material chemical substances, which leads to the depletion of aluminum elements and produces slag.
- Produce hard points in the casting parts, which is harmful to the post-production processing and polishing.
- Enhances the ductility of aluminum alloys. The solubility of iron in the zinc solution increases with temperature, and each temperature shift of the zinc solution in the furnace will result in either over-saturation of the iron content (when the temperature decreases), or unsaturated fat (when the temperature increases). When the iron content is over-saturated, the iron in the over-saturated state will reflect with the aluminum in the aluminum alloy, resulting in a higher slag volume. When the iron content is unsaturated fat, the leaching of the aluminum alloy to the zinc pan and gooseneck raw material may be raised to return to saturation. A mutual result of the two temperature shifts is finally leading to the depletion of the elemental aluminum, generating a large amount of slag.
Conclusion
For more information about the aluminum die casting market,die casting tool material,materials used in die casting, we are glad to answer for you.